GoVetteGo
Well-known member
I have been stick welding for years. I traded for a Snap On Mig welder a few years back and now have an application for it. The #4 body mount bracket on the passenger side of my Darth Vader Vette is toast.
I played around with the MIG welder a bit yesterday using a couple pieces on 1/8" angle iron.
Please look at the picture and tell me if I am on the right track. The following picture is what I did. A was my first attempt and D was the final effort.
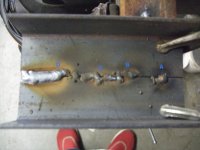
With the stick welder, I would adjust the amps to the size rod I was using. My thought with the MIG welder is I have to adjust the heat level with the wire speed - which is what I did. Weld, adjust, weld, adjust until I got to the last pass.
Appreciate your input.
John
I played around with the MIG welder a bit yesterday using a couple pieces on 1/8" angle iron.
Please look at the picture and tell me if I am on the right track. The following picture is what I did. A was my first attempt and D was the final effort.
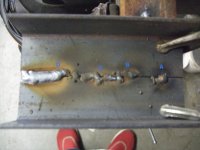
With the stick welder, I would adjust the amps to the size rod I was using. My thought with the MIG welder is I have to adjust the heat level with the wire speed - which is what I did. Weld, adjust, weld, adjust until I got to the last pass.
Appreciate your input.
John