enkeivette
Well-known member
- Joined
- Mar 30, 2008
- Messages
- 990
I'm putting a 74 corvette bumper on my 78 body. I like the look of it better because it doesn't have those ugly bumperettes. I'm going to get rid of the seam and I need to fill in the large gap where the step from the old bumper used to be.
Notice the step in the later bumper.
...........................Step
.............................V
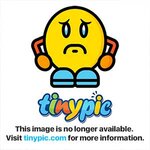
How do you guys think I should fill in that space? I'm thinking about stapling a piece of matte 1/2" below the surface, laying resin over it, then filling it in with shortstrand fiber polyester resin filler.
I also need to delete the sidemarker recesses. I was thinking about filling them in the same way.
Notice the step in the later bumper.
...........................Step
.............................V


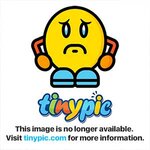
How do you guys think I should fill in that space? I'm thinking about stapling a piece of matte 1/2" below the surface, laying resin over it, then filling it in with shortstrand fiber polyester resin filler.
I also need to delete the sidemarker recesses. I was thinking about filling them in the same way.