vette427sbc
Well-known member
Got my rod ends in today and my hex tube stock should be here tomorrow.
I went with FK bearings RSMX series. .625" hole and 3/4-16 thread with a PTFE liner. They have a 40,000 radial load. Ill be using these on everything except the toe control. The hex tube is 6061 aluminum 1" with a .5" ID. I got 6 feet, which should let me do one side of the car with a bit to spare.
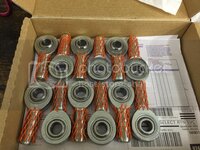
I went with FK bearings RSMX series. .625" hole and 3/4-16 thread with a PTFE liner. They have a 40,000 radial load. Ill be using these on everything except the toe control. The hex tube is 6061 aluminum 1" with a .5" ID. I got 6 feet, which should let me do one side of the car with a bit to spare.
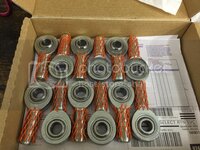