Fuelie74
Well-known member
I have never really worked with fiberglass and need to do some glass work on my 74's floorboards. I want to cut out a small section and move it back to make more room for my transmission yoke after doing a trans swap. I also have a few cracks that need to be repaired. So is matting and resin all I will need and what is the best type of resin to use? Any other advice would also be great!
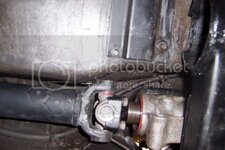
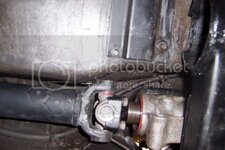