I´ll keep the photos coming, thank´s for the encouragement Kid Vette
So, after reading a lot of posts at different forums I thought it would be a good idea to buy a rack and pinion steering system. The old system was leaking badly but it actually wasn´t too sloppy. I was a bit surprised during my first drive ever in a Corvette that the steering had such a nice and precise feeling after +40 years.
Bought a rack and pinion system from a well known company (I´ll leave the companys out) and the first surprise came when I opened the box. The tie rods were in bare aluminum and machined at each end. Not at all the appeareance shown in adds on the net:crap: Sent an email with a question regarding this and quickly got an answer that they had two suppliers for that part. Acceptable explanation, I´m fine with that. Good to get a quick respons anyway.
Next surprise was the finish of the rack unit. Painted with a silver spray over the old paint which had not been removed:crap: Also something I can fix but irritating.
The third surprise was the orientation of the oil tubes on the rack. Probably what the rack was equipped with from the beginning. I would have expected at least new lines orientated correctly with a minimum quantity of bends. I even had to rebend the tubes to get them away from the oil pan:crap:
Started to test assemble the welded brackets on the frame and the left side did not fit. As seen on the photo the angle between the main plate and the support plate is incorrect. Not possible to assemble.:crap:
Tested the right side and it did fit correctly. Then I tried to pull at the lower end of the bracket where the rack assembles and the bracket moved considerably even with a light pull:crap: No way I would get on to the high way with that connection.
So, what to do about this? I cut the left side connection apart and rewelded it to one single unit modified to fit the original connections. Nothing complicated.
The right side was a bit more complicated. I machined a thick steel plate and made 4 threaded holes in it. Welded it to the underside of the frame (well, it took me a few hours to get it correct) and modified the bracket with support plates so it could be bólted to the frame as one unit. Now free from flex and securely bolted to the frame.
I have no doubt that the rack system would have worked right out of the box (with som tweaking), but I really do expect more when I buy expensive parts like this. I also do understand that Corvettes are not all the same so it is probably difficult to manufacture a system that fits perfectly on all cars.
The non fitting left side bracket
Modified left side bracket
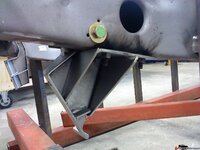