With closed-wheelers the situation might appear to be simpler, but can in fact be more complex than open-wheelers. Enveloping body work obviously shrouds the wheels from much of the air that they would otherwise encounter; and this is the basic reason we expect a lower drag from a closed-wheeler, but air still enters the wheel wells from in front, underneath and out to the sides, and how it is dealt with can have significant effects. It is also the case that rotating wheels can act as pumps in semi-enclosed wheel wells, an effect that increases with vehicle speed to the extent that air can be drawn
into the wheel wells from the rear and pumped out at the front, according to one former wind tunnel operator writing to
Racecar Engineering.
Often such efforts to improve things will involveducts, cutaways and louvers that in general help air to escape from wheel wells. The louvers on top of sports prototype wheelarches are present to help reduce the differential that can exist between the low static pressure over such a curved wheelarch compared to the the static pressure in the wheel well, a potential source of undesirable lift. The cutaways often present on the vehicle sides behind the front wheels also assist air to escape not only from the wheel wells, but also from under the front of the car. As these features often work in concert with front splitters and diffusers, providing an exit for air that has been exploited further forwards on the car. [\QUOTE]
Simon has now images other than the word picture above. I'll focus initially on Radiator Airflow, and as I find the other (louver) details will bring those in too.
Internal cooling is the single largest contributor to drag:
Below is a crude representation of C3 radiator flow:
But it can be adjusted through configuration changes/modifications. Just the orientation for the radiator and exhaust air can make a difference:
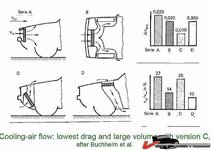
Note that "C" has lowest drag and highest volume of air of the 4 configurations.
Here is a good example of radiator ducting (on a C-5):
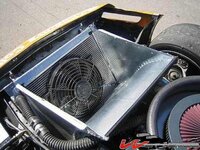
Some work could be made to improve its flow - but better than stock configuration.
An example from John Greenwood:
When I say "work to improve the flow" note the relationships described below:
Full open exit is not optimum, but closed in relationship to the entrance. I recall 50%, but may be off on that. You can imagine it could/would act as a venturi, but with a choked exit to keep exhaust flow speed up. The venerable P-51 Mustang used a variable exit on the radiator (located under the belly) and made it pump as a small "jet" increasing speed, by using the heated air from the oil cooler(s).
NOTE: That would constitute "Active Aerodynamics" and may not be permitted by some race organizations.
NOTE: it did offset the drag due to cooling by about 90%. SIGNIFICANT when you look back to figure 1 above.
Hope this is at least mildly interesting and useful.
Cheers - Jim