SuperBuickGuy
Well-known member
axle bracket time... first, conceptualize
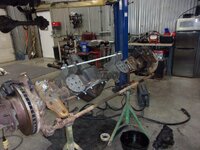
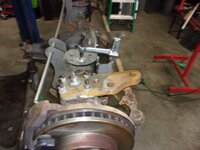
explanation
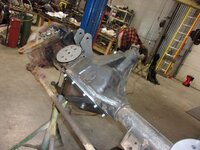
I could have welded the brackets to the tube - not the cast steel of the housing - however, that'd put the arms outside the frame and more in harm's way. Also, with this I can simply use GM shocks that are the right length... and no, I'm not afraid of welding to cast steel - I did on my FJ40 and 8 years later, it's still holding just fine.
then cad
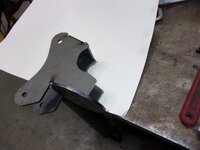
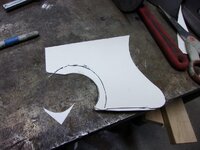
mark
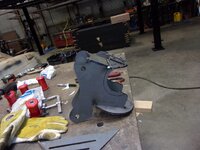
then cut
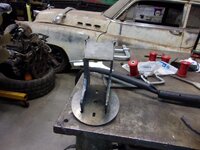
then fit
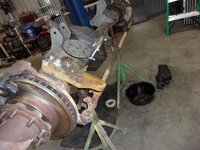
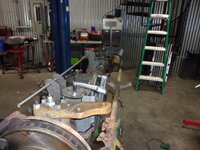
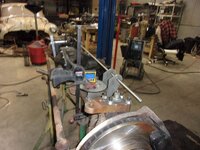
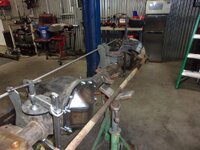
so Amazon ... they 'recalled' the first steering box and now it looks like they're going to do it again.... it hasn't been sent .... fme.The problem is I need a box to continue mounting brackets...
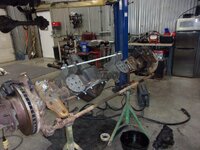
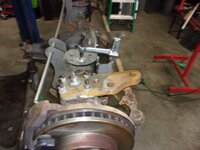
explanation
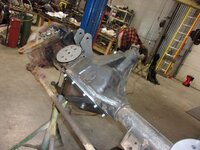
I could have welded the brackets to the tube - not the cast steel of the housing - however, that'd put the arms outside the frame and more in harm's way. Also, with this I can simply use GM shocks that are the right length... and no, I'm not afraid of welding to cast steel - I did on my FJ40 and 8 years later, it's still holding just fine.
then cad
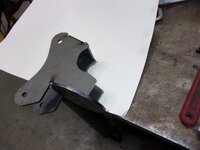
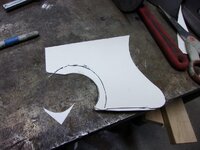
mark
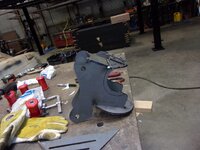
then cut
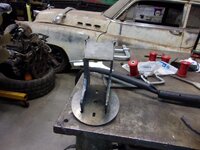
then fit
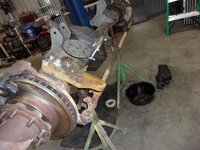
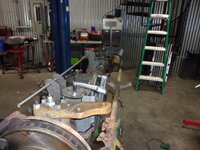
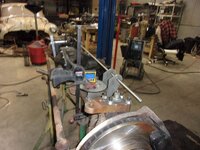
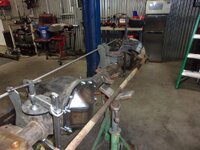
so Amazon ... they 'recalled' the first steering box and now it looks like they're going to do it again.... it hasn't been sent .... fme.The problem is I need a box to continue mounting brackets...