rtj
Well-known member
- Joined
- Nov 5, 2011
- Messages
- 3,153
I recently assembled one of Tom's 12 bolt kits. He tuned the posi, fitted the stub axles, and blended out the edges on the posi for a reasonable price. The details were posted on another forum.
I get a lot of good info from this site, so I figured I'd post some photos from the build up of the entire IRS. It's the complete Tom's kit, and I'm going to do a few more things.
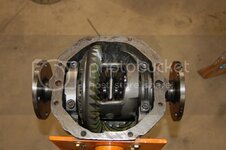
Final photo of the assembly.
Here's the cross member tig'ed up. Hard to clean real good, and the place I went to get gas pushed an argon mix, when I asked for straight argon. I took the mix, but think it was a mistake.
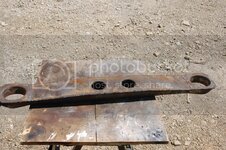
Another thing going in this is the adjustable toe mentioned in one of the PDF's in the Tech section. I got some grade five 3/4" bolts and nuts and have it mostly machined up. Here's the first couple of pieces. I"ve tried machining grade 8 before, and it was a pain, the grade 5 was not too bad. I'll need to order some extra long through bolts, this short one is just for fitting.
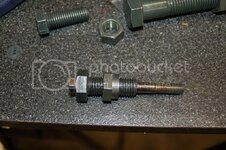
I think this will be far stonger than the standard bolt and shims. I will eventually work on the engine, and figured I'd plan for it.
A few other things on the list, lots of gussets, solid aluminum bushings on the cross member and pinion snubber, new 3.5 in driveshaft with 1350 u joints....
I get a lot of good info from this site, so I figured I'd post some photos from the build up of the entire IRS. It's the complete Tom's kit, and I'm going to do a few more things.
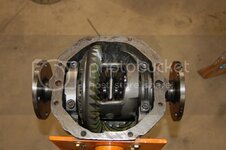
Final photo of the assembly.
Here's the cross member tig'ed up. Hard to clean real good, and the place I went to get gas pushed an argon mix, when I asked for straight argon. I took the mix, but think it was a mistake.
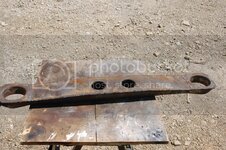
Another thing going in this is the adjustable toe mentioned in one of the PDF's in the Tech section. I got some grade five 3/4" bolts and nuts and have it mostly machined up. Here's the first couple of pieces. I"ve tried machining grade 8 before, and it was a pain, the grade 5 was not too bad. I'll need to order some extra long through bolts, this short one is just for fitting.
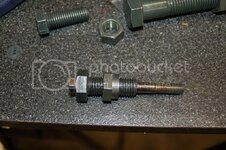
I think this will be far stonger than the standard bolt and shims. I will eventually work on the engine, and figured I'd plan for it.
A few other things on the list, lots of gussets, solid aluminum bushings on the cross member and pinion snubber, new 3.5 in driveshaft with 1350 u joints....