denpo
Carburated Nihilist
Good and bad news
Yesterday was a bag of mixed feeling.
The good : my heater core arrived, the tracking still tells it's at the departure post office, I guess you have to take those with a grain of salt.
This is a brand new one, bought from our trusty Willcox but never installed. At 25$ that's a steal.
Now I can reassemble my interior once for good.
The bad : I kept of removing the paint and what's under is worrying.
You see those two area near at the back of the front clip where there's still the top black paint layer:
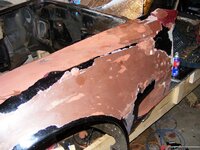
Well, turned out under that there is a mofo thick layer (around 1/16") of soft yellow repair crap stuff, and under that the fiberglass is bible paper thin.
I'll post picture this evening.
When I talked about the 16 layers of paint to my friend (actually 18, the pink-salmon stuff on the picture turned out to be one of the two last layers before I actually reached the fiberglass) they joked about the fact I'm removing structural strength to be body, looks like it was not such a joke afterall. *sigh*
Yesterday was a bag of mixed feeling.
The good : my heater core arrived, the tracking still tells it's at the departure post office, I guess you have to take those with a grain of salt.
This is a brand new one, bought from our trusty Willcox but never installed. At 25$ that's a steal.
Now I can reassemble my interior once for good.
The bad : I kept of removing the paint and what's under is worrying.
You see those two area near at the back of the front clip where there's still the top black paint layer:
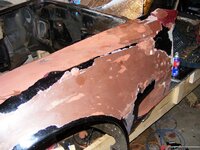
Well, turned out under that there is a mofo thick layer (around 1/16") of soft yellow repair crap stuff, and under that the fiberglass is bible paper thin.

I'll post picture this evening.
When I talked about the 16 layers of paint to my friend (actually 18, the pink-salmon stuff on the picture turned out to be one of the two last layers before I actually reached the fiberglass) they joked about the fact I'm removing structural strength to be body, looks like it was not such a joke afterall. *sigh*