bobs77vet
Well-known member
house quieted down early tonight....so that means when the Boss goes to sleep its play time...about 1.5 hrs
the fender still needs some more love
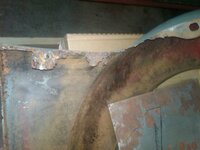
just make up a new piece to slip into place
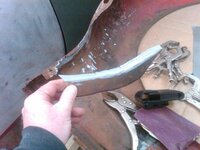
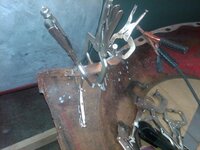
of course I had two holes top side, so I made the repair piece to cover this area also
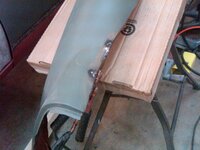
of course theres always one more rusty spot
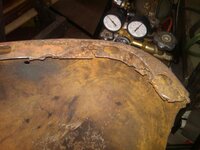
too late to do any grinding
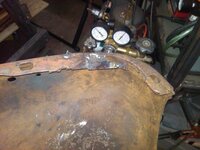
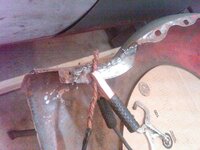
the fender still needs some more love
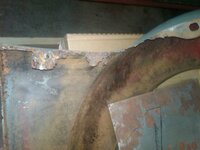
just make up a new piece to slip into place
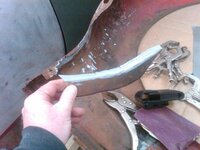
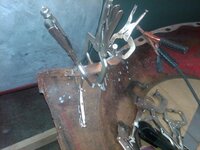
of course I had two holes top side, so I made the repair piece to cover this area also
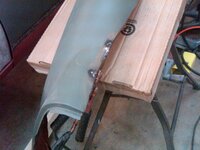
of course theres always one more rusty spot
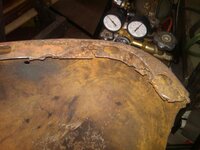
too late to do any grinding
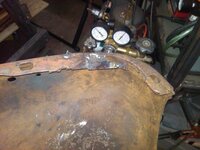
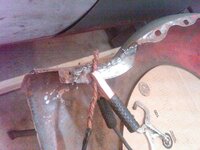