bobs77vet
Well-known member
I trully do like the fabrication aspects of the restoration, making that temp scuttle was a lot of fun for me.
I got some electrical goodies today so spent some time looking and figuring..
real battery cable #1 welding wire
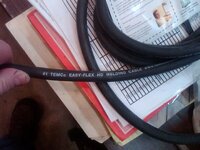
old vs new
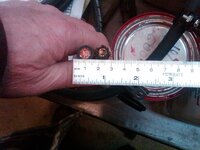
any body know if the rear wire harness is bigger then a rectangular 1/4 x 1/2" opening...if so i will be making some new double P clips
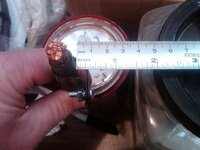
this is a sweet fit 1/2" insulated single p clip. i will use this at the end where the battery cable has a p clip on one of the floor board screws
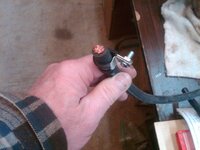
so lets play around with terminating the ends on the old scrap cable becasue of the gauge difference the scrap piece had the insulation still on it. it would have shrink wrap on it for the final version
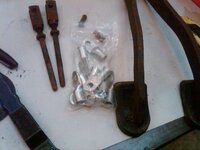
i havent done this in a while and with most things its takes a couple of practice trys to remember how to do it.
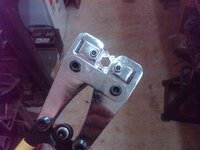
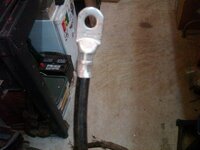
i tried pulling this apart by clamping it in the vise and i could not pull it apart
I got some electrical goodies today so spent some time looking and figuring..
real battery cable #1 welding wire
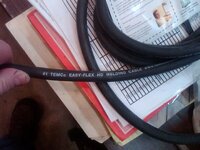
old vs new
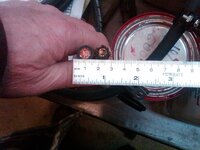
any body know if the rear wire harness is bigger then a rectangular 1/4 x 1/2" opening...if so i will be making some new double P clips
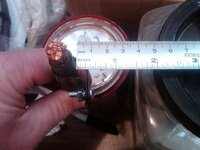
this is a sweet fit 1/2" insulated single p clip. i will use this at the end where the battery cable has a p clip on one of the floor board screws
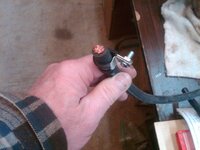
so lets play around with terminating the ends on the old scrap cable becasue of the gauge difference the scrap piece had the insulation still on it. it would have shrink wrap on it for the final version
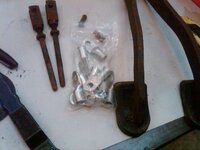
i havent done this in a while and with most things its takes a couple of practice trys to remember how to do it.
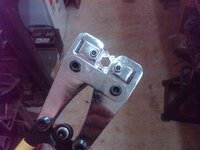
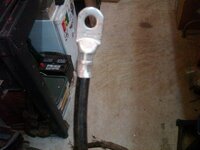
i tried pulling this apart by clamping it in the vise and i could not pull it apart