As you all probably know, I do lots of projects - and because I'm totally ADD I do multiple at a time. Right now I'm doing a 1964 Buick wagon (and I just finished a fuel system on a 70 Toyota FJ40)....
but this I think might be interesting here and I would love to hear opinions - even if it's for depth of knowledge in one place for someone doing something similar.
With that set up, I have a 2004 6.0 LS from a Denali, it's not the high hp one, but its 325 hp was adequate. The Denali was just one, continuous electrical nightmare so it's gone and the motor is here. I was going to just swap cams, I should have left well enough alone but here I am at deciding whether or not to go all in.
The motor had 200k and was starting to show low oil pressure.
here's its test fit
plugs looked fine
started collecting the basics, the oil pan is wayyyy too deep, so it's replaced
flywheel because it was 4L65e now 4L80e
headers
intake because the truck intake won't fit (and I may, in the end not use it)
I hate egr on these things... that coating is egr related
test fit without the pan
I got lucky that this actually fits (it's close to the steering box)
Sig Erson cam
now just swap the pan... just
I bought springs because it's a 200k motor, but this is where it started going sideways (and it was clean inside)
the cam looks like it was literally chattering in the bore....
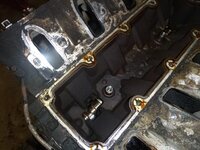
not just that but every rocker is worn
of course, the chain was loose - however I was going to replace the oil pump anyway
between the chattering, the loose rockers, and the strange wear on the cam - my 'line' not pulling the heads was about to get crossed
I had to pull the cam anyway (for the new cam) but I didn't expect literal steps on the cam and it was time to look further
interestingly, the inside of this motor looks good (regular oil changes)
however, if you look close, you'll see where the push rods where hitting the heads
then I pulled the lifters.... very worn
however, the rod and main bearings were perfect
other then the build up due to EGR valve, it looks rebuildable
crank even looks fine
and finally the cam bearings....
I have new heads, but the block came back with egg shaped bores (not much, mind you, but still a .0015 taper and .002 out of round).... I could throw it together, but part of me figures in for a penny I might as well finish it.... cost is roughly 2k for a new rotating assembly with a longer stroke and I could play with the compression ratio if I actually decide on substantial boost .... if I don't stroke it, it's still a balance, rod press and bore but save about 1k ..... and would still get the benefit of playing with the compression ratio...
thoughts?