bobs77vet
Well-known member
well time to get back at it......after contemplating a course of action for a few days I said screw it and just started cutting and welding...
I made an inner brace for the door hinge pillar post to tie the two hinge posts together and welded these bolts at the correct spacing for the brackets
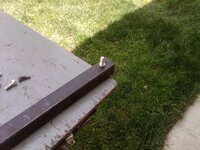
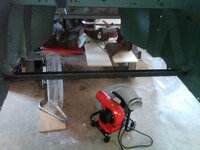
this takes most of the movement out of the doors hinge post
I guess I forgot to take the heads out of the hinges when I drilled out the screws
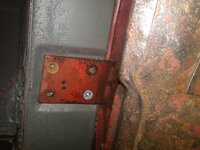
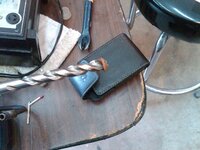
I feel like cutting out rust today
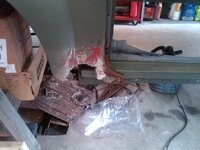
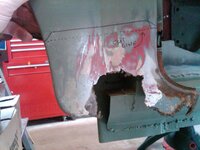
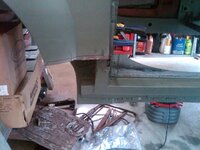
these are just the most of a preliminary fit as you can get
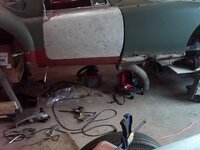
some more cut lines
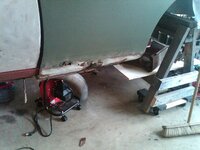
taking car of the inner brace
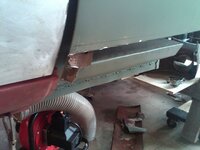
the inner brace cleaned off
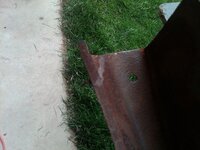
lots more to do here .....but no more rust in this area
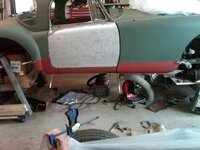
I made an inner brace for the door hinge pillar post to tie the two hinge posts together and welded these bolts at the correct spacing for the brackets
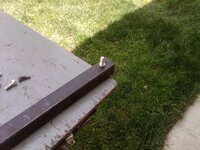
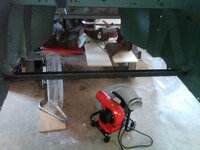
this takes most of the movement out of the doors hinge post
I guess I forgot to take the heads out of the hinges when I drilled out the screws
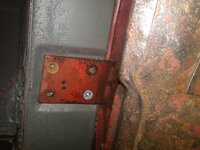
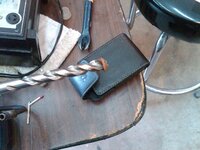
I feel like cutting out rust today
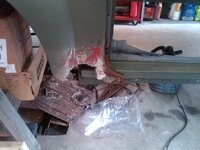
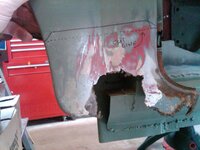
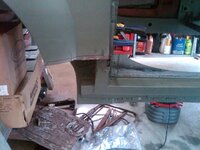
these are just the most of a preliminary fit as you can get
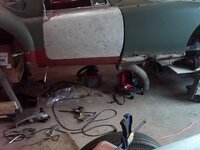
some more cut lines
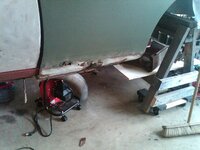
taking car of the inner brace
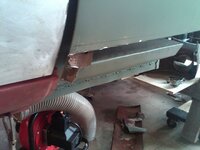
the inner brace cleaned off
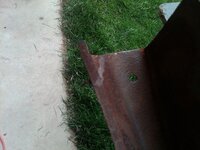
lots more to do here .....but no more rust in this area
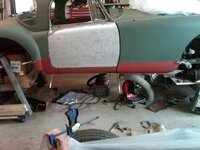
Last edited: