phantomjock
Well-known member
Diy - Ruggles Scales
I bet for the tank of fuel and the trip over to Topeka, you could whip up a set of Ruggles Scales:
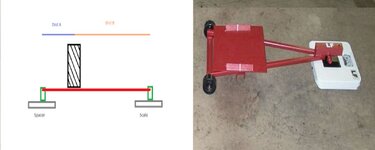
Or just make one and block the other 3 wheels to same height and get your corner weights using just one.
This from the Factory Five Forum:
Timber version:
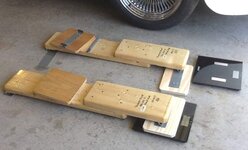
Cheers - Jim
I bet for the tank of fuel and the trip over to Topeka, you could whip up a set of Ruggles Scales:
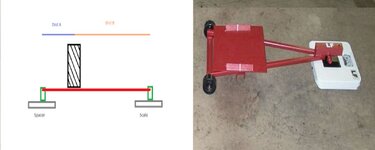
Or just make one and block the other 3 wheels to same height and get your corner weights using just one.
This from the Factory Five Forum:
The theory is that on a level surface with a spacer the same height as the bathroom scale, the ratio of total distance over distance A is your multiplication factor for what your scale reads. [(A + B) / A] = Multiplication Factor
Ex: If distance A is 30 and distance B is 30 (half way between the spacer and scale): (30 + 30) / 30 = 2, so you multiply what your scale says by 2 to get the actual value.
If you want to use a 200lb bathroom scale to weight something with a max weight of 2000lbs, you just need a long bridge between the two plates and set your pivot point with distance A being 1/10th of A + B.
Things to keep in mind:
You need a stable structure with everything level. Its also hard to balance a tire, attached to a car of course, without at least two connecting rods for the tire to sit in. In the idealized form, you would use the centerline of the tire as the distance point, but in reality since the scale side is moving it shifts the contact patch and I dont know if this will change readings since a tire is flexible. For reasonable distances, a reading on the scale with the weight fixed at the inside of the tire vs outside of the tire would cause a huge change.
Your error factor gets multiplied as well. The scale you are referencing says withing .2lbs, which i'm taking to mean +- 0.1lb. If you were to use a 1:10 arm ratio, that error factor gets multiplied by the same value to become +-1lb.
Timber version:
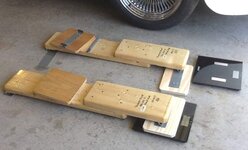
Cheers - Jim
Last edited: