On to the flywheel and clutch.
I ordered a SFI certified flywheel when i bought the Tremec TKO 600 gearbox together with a heavy duty clutch.
The flywheeel is made in USA and it is a well known quality brand. The instruction said to check unbalance before assembly, even although it was already balanced. Shown by a big hole drilled in the flywheel.
So, I started by measuring the complete flywheel in the digital measuring machine at my work.
With the guide diameter for the crankshaft as the reference surface, I measured runout of the inner diameter of the friction surface and the runout of the outer diameter (just below the starter ring gear) in relation to the guide diameter.
The result was quite shocking to me:shocking: The measuring machine showed a total runout of 0,002" (0,05mm) on both diameters in relation to the guide...
This means that the larger part of the mass on the flywheel is acting as an unbalance weight. This is really not an indication of high tech and quality in my world.
Of course, the unbalance is fixed by the balancing operation but it would be better to do a more accurate machining from the beginning.
Well, I modified a balancing shaft that I had been using for snowmobile clutches with a small press fit to the flywheel guide diameter and balanced it to within approx. 0,1grams (0,00353 Ounces).
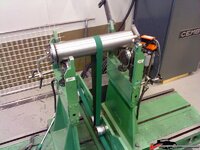